Benefits, Markets & Applications
Cost effective, bespoke waste free parts
Metal Injection Moulding (MIM) is a manufacturing process that involves manipulating metal powders to behave like a plastic by mixing them with polymer binders to form a feedstock. This feedstock is used to injection mould net shaped, precision components.
Parts are then thermally processed to remove the binder system and finally they are sintered to a high density metal component with comparable mechanical properties to wrought materials. Intricate and complex 3D geometries that in the past have been either very difficult or very costly to produce through traditional manufacturing methods such as 5 axis CNC machining, can be readily achieved with metal powder injection moulding and at significantly reduced prices and lead-times.
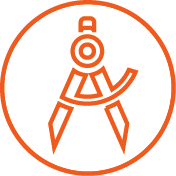
In house production
CMG facilitates the entire MIM process in-house, enabling significantly reduced lead times when compared to manufacturing using more than one contractor.
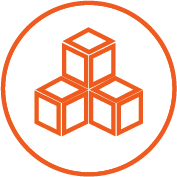
Small and Large annual volumes
MIM is effective in producing complex components in annual volumes tailored to each individual product. Our MIM process is suitable to provide both small or large annual volumes of components, while maintaining cost effectiveness.
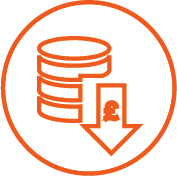
Reducing costs
Intricate and complex components
that have previously been difficult or costly to produce through traditional manufacturing methods can be achieved at significantly reduced prices.

No waste
CMG are the only MIM company in the UK to facilitate the complete MIM process in-house – a manufacturing method for metal, which is used to produce precise, complex parts in large quantities with low waste.
Markets & Applications
Supplying parts worldwide
Making intricate, vital parts for life-saving ventilators
Case Study: Saving lives with MIM for crucial Covid-19 ventilators
Servomex’s sensor technology brand Hummingbird required support to manufacture vital parts for its Paracube oxygen sensor. The sensor is used in ventilators for treatment of severe respiratory diseases and disorders exacerbated by COVID-19.
How would you explain MIM in a nutshell?
Metal Injection Moulding (MIM) is a manufacturing process that involves manipulating metal powders to behave like a plastic by mixing them with polymer binders to form a feedstock. This feedstock is then used to injection mould net shaped, precision components for use in a wide range of industries. Visit our Metal Injection Moulding page to find out more.
What materials can be Metal Injection Moulded?
MIM components are available in various materials – please visit the Material & Properties section for more details.
What applications are MIM parts used in?
Our MIM process is now becoming widely accepted as the standard manufacturing technique within a number of industry sectors – our Markets & Applications section above has more details.
What are the strength properties compared to the wrought material?
The strength and performance of parts made using metal injection moulding are comparable to those of wrought and cast components.
What is the average density of MIM parts?
Generally after the sintering stage the theoretical density of the components we produce will be controlled within the range of 95 – 98% dense. Find full details on our Material & Properties section.
Are MIM parts porous?
Due to the nature of the MIM process, there will be some porosity left in the component after the sintering stage, however, what porosity is left will be very fine and isolated, giving density in the region of 95-98%. Even machining or casting will not give 100% dense parts as there will often be inclusions.
What are the minimum volumes viable for Metal Injection Moulding?
MIM is most effective for small, complex components in annual volumes of 1000 or more (although if the part is particularly complex and expensive MIM could still be cost effective for volumes of 500 or more).
Is MIM CMG Technologies' core business?
Yes, Metal Injection Moulding is our core business and we are fully equipped to keep every stage of the MIM process in-house. Find out more about CMG Technologies.
What Quality Standards does CMG Technologies work to?
CMG Technologies is ISO 9001-2008 accredited and we work in accordance with our tight Total Quality Fundamentals.
What equipment does CMG Technologies have?
Our volume capability is underpinned by: six Moulding Machines, five Debind Ovens, four Sintering Furnaces, in house Polishing Capability, fully equipped Tool Room with an AutoCAD System, Mitutoyo Vision Measuring Machine, and various Sizing and Measuring Tools.
Does CMG Technologies offer design advice?
Yes, we offer support and design advice on new and ongoing projects, and we maintain a high level of communication between both parties throughout all MIM projects.
Do CMG Technologies make their tools in house?
Yes, we design the tools in house on our AutoCAD based system and build the tools in our fully equipped, well maintained tool room. The tool comes with a lifetime guarantee so all maintenance and repair is carried out at our cost.
What feedstock does CMG Technologies use?
We compound our own feedstock in house. Each mix is custom developed by our metallurgist to ensure it will give us the shrinkage rates required to achieve the parts final dimensions. We also use the commercially available Catamould feedstock. Find out more about feedstock.
My question has not been answered - who shall I contact for more information?
Please contact our sales office at: sales@cmgtechnologies.co.uk or phone 01394 445100
Why CMG?
We pride ourselves on the excellent relationships we forge with our customers, becoming an extension of their businesses with friendly and clear communication. By drawing upon more than 25 years’ experience using the MIM process to facilitate this entirely in-house in the UK, we produce parts that meet client specifications in a professional and timely manner.
Rachel Garrett, Managing Director
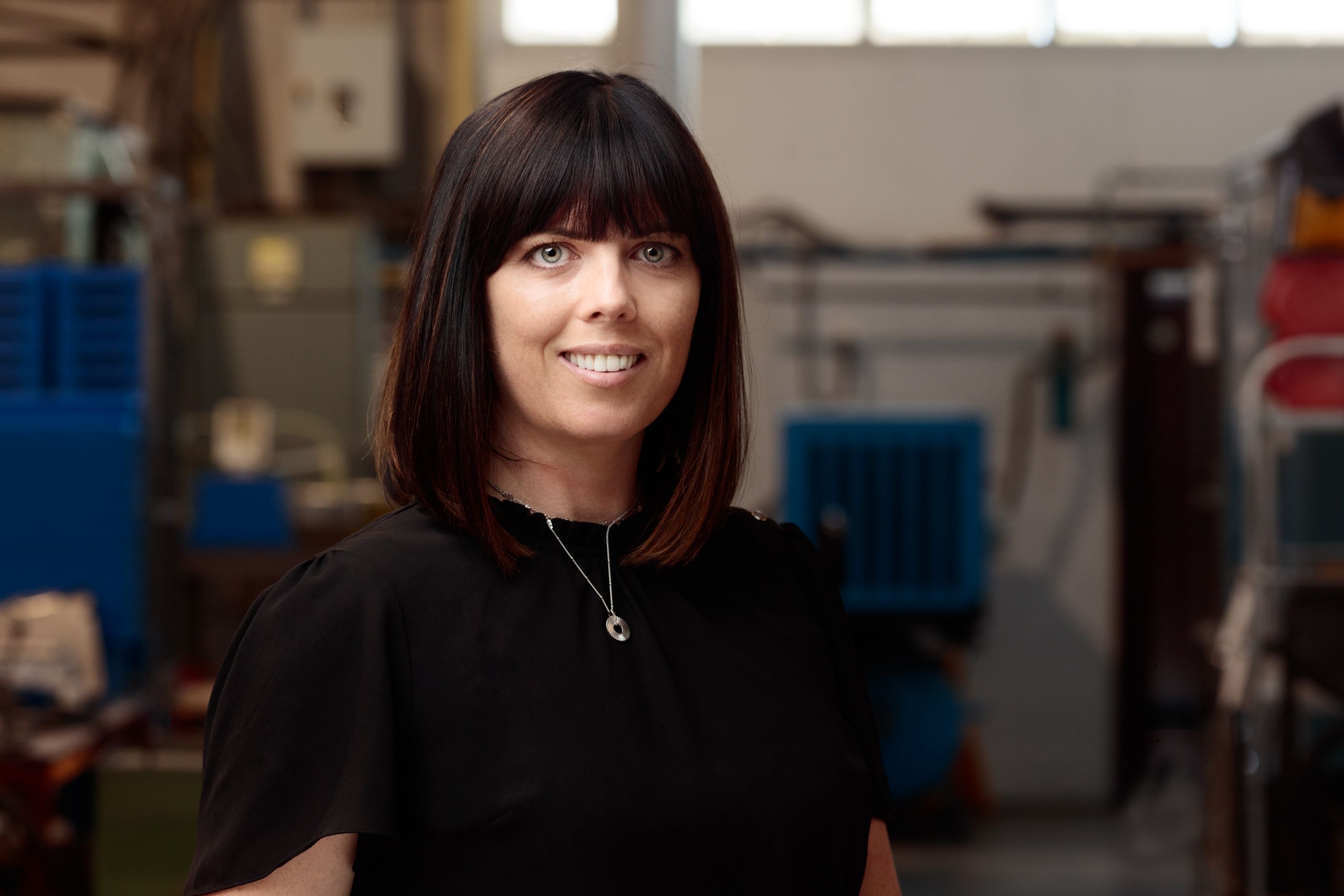
Subscribe to our newsletter for product and industry innovations.