Design, Materials & Properties
In house capabilities at CMG Technologies
At CMG Technologies, our entire product design and development process is completed in-house in the UK. From the tool design and build, to compounding the feedstock, through to the final sintering stage. Completing everything in-house allows us to have maximum control at every stage. Therefore, it results in consistency and dimensional repeatability within our products. The parts we produce are of unrivalled quality and are ISO9001-2015 accredited.
Material & Properties
Supplying parts worldwide
CMG is constantly developing new materials both independently and in partnership with our customers and suppliers – if we can source a material in powder form, we are willing to run trials.
The density and performance of MIM parts is comparable to those of wrought and cast components. As with CNC machining or casting, components made using the MIM process may contain some porosity, but this will be very fine and isolated. Generally after the sintering stage the surface finish is around 0.6-0.8 microns and the theoretical density of the components we produce will be controlled within the range of 95 – 98% dense. CMG Technologies manufacture parts from micron powders, enabling us to produce parts with wall sections as thin as 0.5mm which are hermetic to greater than 10-10 torr for applications in Gas Analysis and Hermetic Packaging.
Material |
Properties |
300 and 400 series stainless steel |
We use 300 grade stainless steels due to their excellent strength and toughness. The austenitic material is non-magnetic and very durable. The 316L grade, which is very resistant to corrosion due to its low carbon content, is used in a wide range of MIM components. Contrary to the 300 grades, the 400 series has a higher carbon content. These grades tend to be harder in their sintered form. They are stronger and can be heat-treated for extra hardness and strength. |
Stainless steel 17-4 |
It provides an outstanding combination of high strength, good corrosion resistance, and good mechanical properties. Through precipitation-hardening, a heat treatment technique, the material can be made even harder and stronger. |
Kovar |
This MIM alloy – consisting of iron, nickel and cobalt – is most commonly used in electronic applications. Traditionally, Kovar is used for metal-to-glass sealing because of its low coefficient of thermal expansion. The material is also magnetic over a high temperature range. |
2% Nickel Iron |
This has excellent mechanical properties for all types of high load applications in heat-treated form. It boasts good strength and fatigue resistance. It is commonly used to improve surface hardness and corrosion resistance. |
Iron |
Iron has very similar properties to nickel iron but has slightly less strength. However, this material has outstanding magnetic properties. |
Copper | As a pure metal, it is suitable for thermal applications because of its high thermal conductivity. Complex heat sink components with thermal features can be manufactured. Copper is also a useful MIM material for electrical circuits. |
Ceramic |
Alumina ceramic (99.7%) is used for MIM products that require good wear and corrosion resistance. It is useful for electrical insulating bodies, chemical operations, industrial machinery, and the vacuum industry. Ceramic has a very high maximum working temperature and can be heated up to 1,500°C |
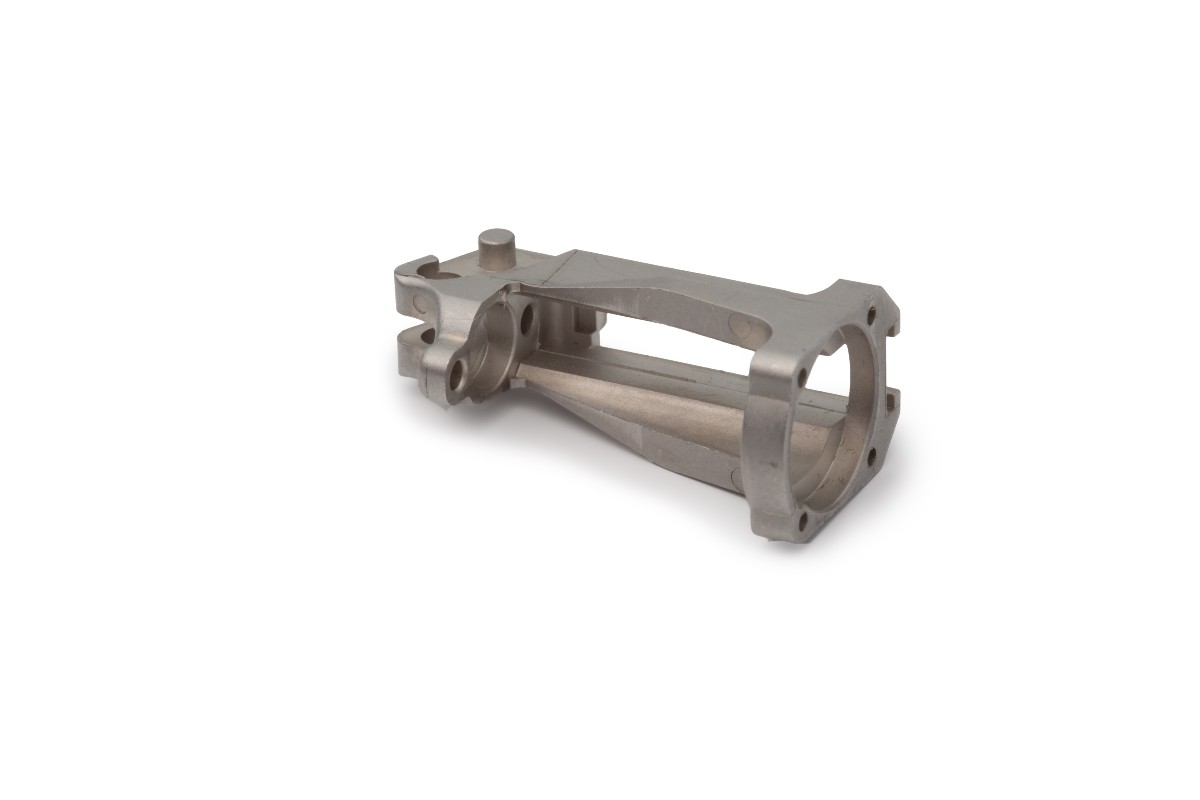
What is MIM?
Metal Injection Moulding (MIM) is the answer to reducing costs, lead-times and the environmental impact for thousands of products. By manipulating metal powder to behave like plastic, it allows the creation of complex machined parts.
Find out more about MIM and the MIM process by downloading our fact sheet.
Design Guidance
Our MIM process allows for the creation of intricate components to benefit products of all types. From making cost-effective and complex 3D geometries to adding logos and texts in one operation. We can also produce parts to tight tolerances, the standard is +/- 0.5% but this can be improved with secondary operations. Our standard surface finish (RA 0.6-0.8) can also be improved to RA 0.2-0.4 with polishing.
You can find out more about our design capabilities by downloading the fact sheet below.
Customer process timeline
Our promise to you
CMG Technologies aims to provide quotes for our product design and development within 3-5 working days. Work on tool design will begin once all design fundamentals are accepted. Designing tools and getting approval takes between 1-2 weeks. The manufacturing of tools takes between 4-6 weeks and samples will be provided between 2-3 weeks. To find out more about the lead-time, please don’t hesitate to get in touch.
Subscribe to our newsletter for product and industry innovations.