Problem:
The UK’s leading cable assembly manufacturer, Rockford, required bespoke levers compatible with BAND-IT tools.
While the company were able to manufacture the parts using their in-house computer numerical control (CNC) process, it proved costly.
Rockford needed a cost-effective solution which still provided high-quality results.
Solution:
CMG Technologies are proven experts in optimising the use of fused filament fabrication (FFF) 3D printing to create parts.
Head of 3D Printing, Dr Samuel Wilberforce, used the manufacturing process to develop parts which met the needs of the client.
Summary:
CMG Technologies carried out the small series production of bespoke layers to build up the levers.
To achieve the desired durability, the levers were manufactured using CMG Tech-X 316L stainless steel filament.
They were printed with a triangular infill of 35% on 3DGence’s MP260x, so the parts were both lightweight and functional.
Find out more about CMG Tech-X filaments
The green parts were then debound using industrial standard equipment, before being sintered at 1250°C under 100% hydrogen gas. The sintered parts achieved a dimensional tolerance of within 1% of the required dimensions, therefore proving the accuracy of CMG Technologies’ printing and sintering process.
Finally, the levers were tumble-polished to achieve a quality finish.
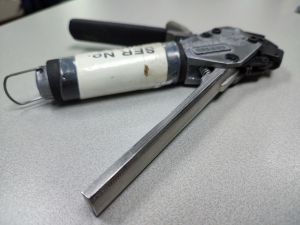
Lever in use (courtesy of Rockford)
Case study:
Rockford, based in Rendlesham, is the UK’s largest independent provider of wiring, interconnect and system solutions.
The company works directly with the aerospace, defence and industrial markets, with a reputation of delivering high-quality products.
A spokesperson for the company said: “The replacement handles that CMG have produced for us are to a very high standard. No modification was needed at all. Although as a company we do have our own machining facilities, manufacturing on a CNC mill was not cost effective.
For small batch parts that need to be functional in a real-world environment, I cannot see a better option. Our thanks to the team at CMG for their professionalism and support.”
If you are interested in metal 3D printing, email 3dprinting@cmgtechnologies.co.uk.